Summary
Sector: Renewable Energy
Software: SolidWorks, Matlab
Project Time: 15 weeks
A novel approach to cooling the stator of large turbine machinery was introduced and analyzed as part of a research paper with the BEEM lab at the University of Colorado Boulder. The system was analyzed as part of an offshore wind turbine generator and heat exchange system. The goals of this project were to:
1. Come up with new ways of cooling generators with additive manufacturing
2. Analyze and prove the effectiveness of the system
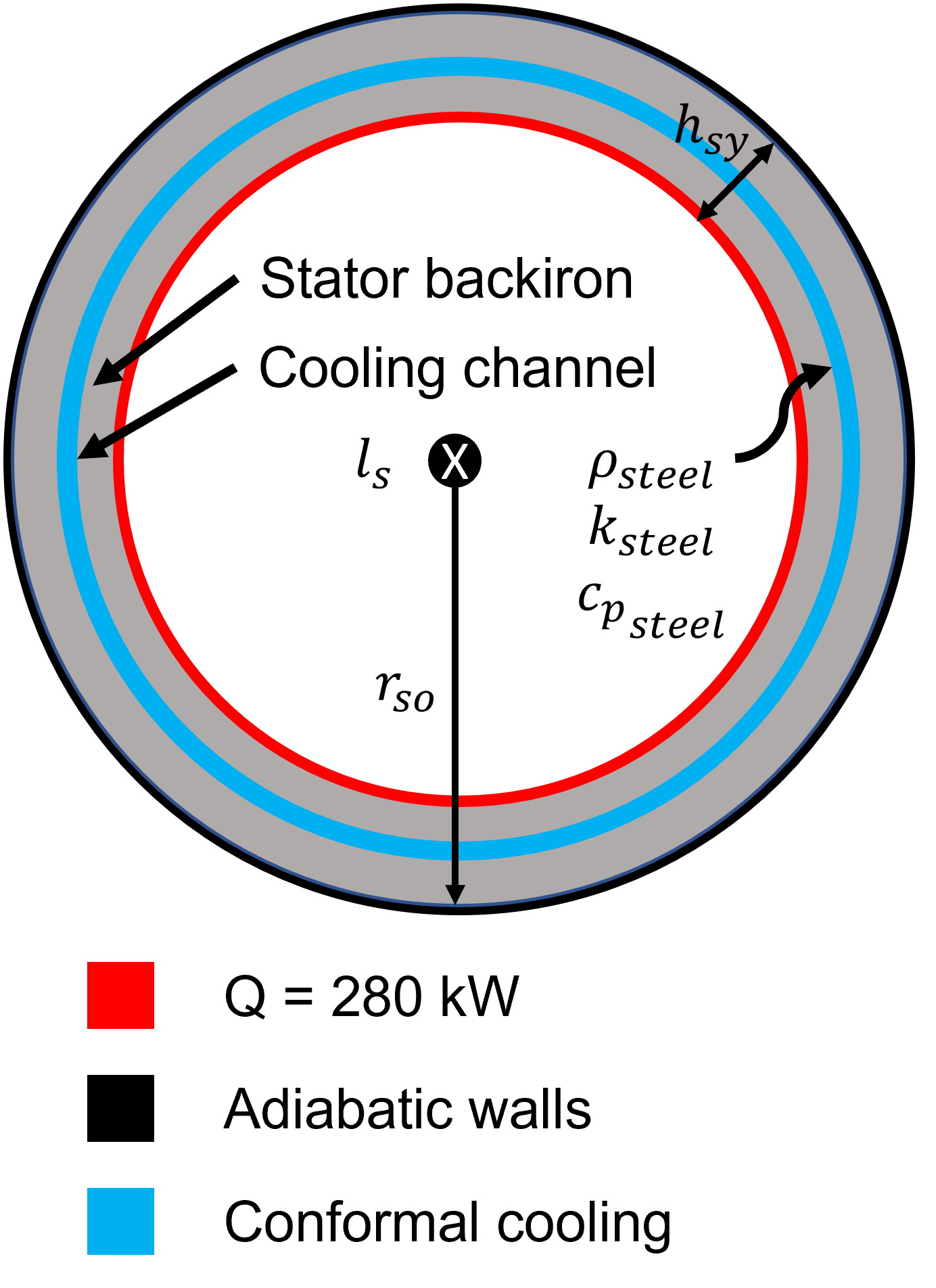
Design Process
The fist task was to understand how a generator works, specifically the thermal interactions between the stator, wires, and magnets. *This figure was created by my supervisor on the project, Austin Hayes.
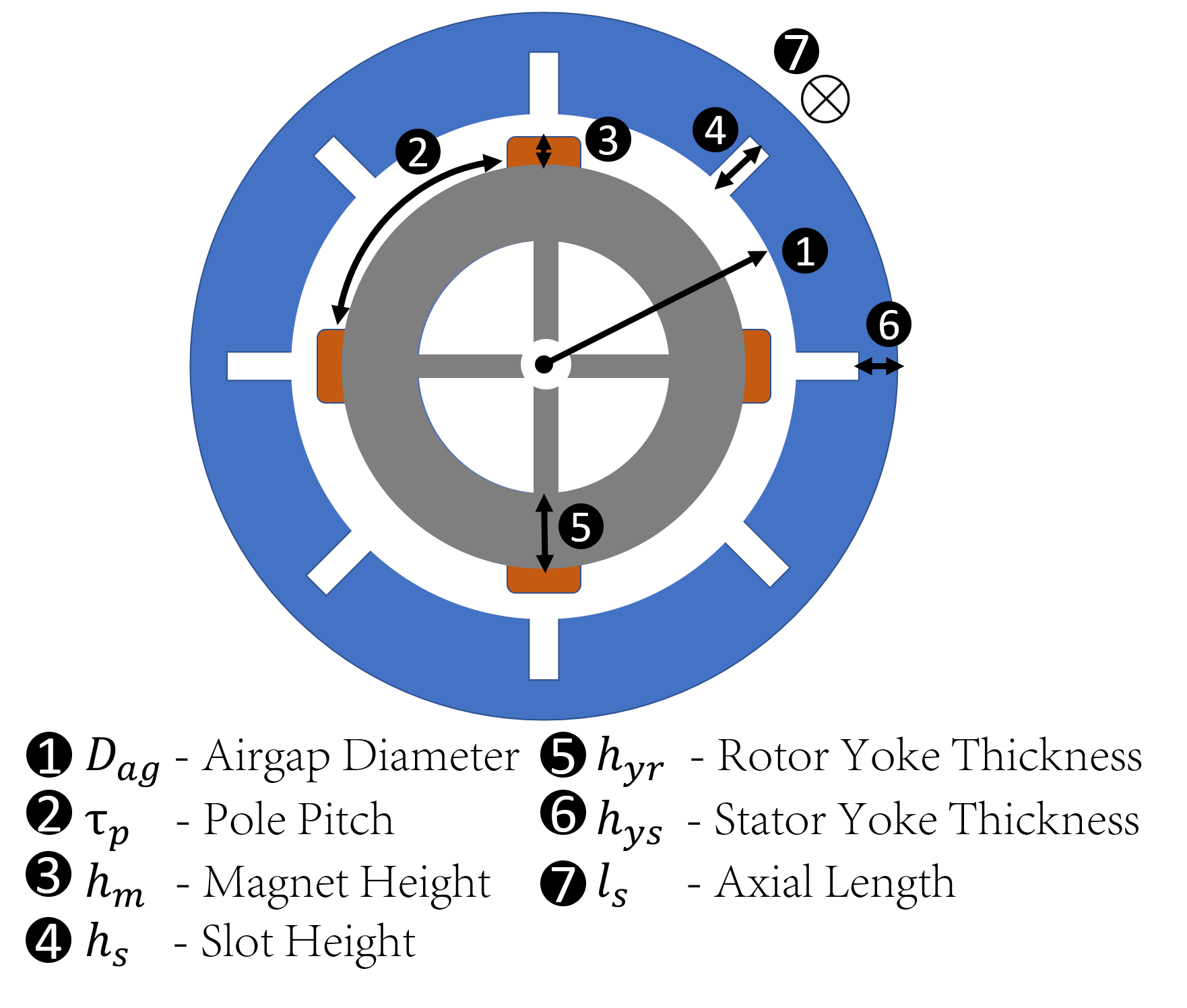
Three Cooling Channel Designs
I generated many ideas for cooling channel designs and picked these three to move forward with based on previous cooling channel designs and intuition. The three designs were honeycomb, series, and parallel channel layouts.
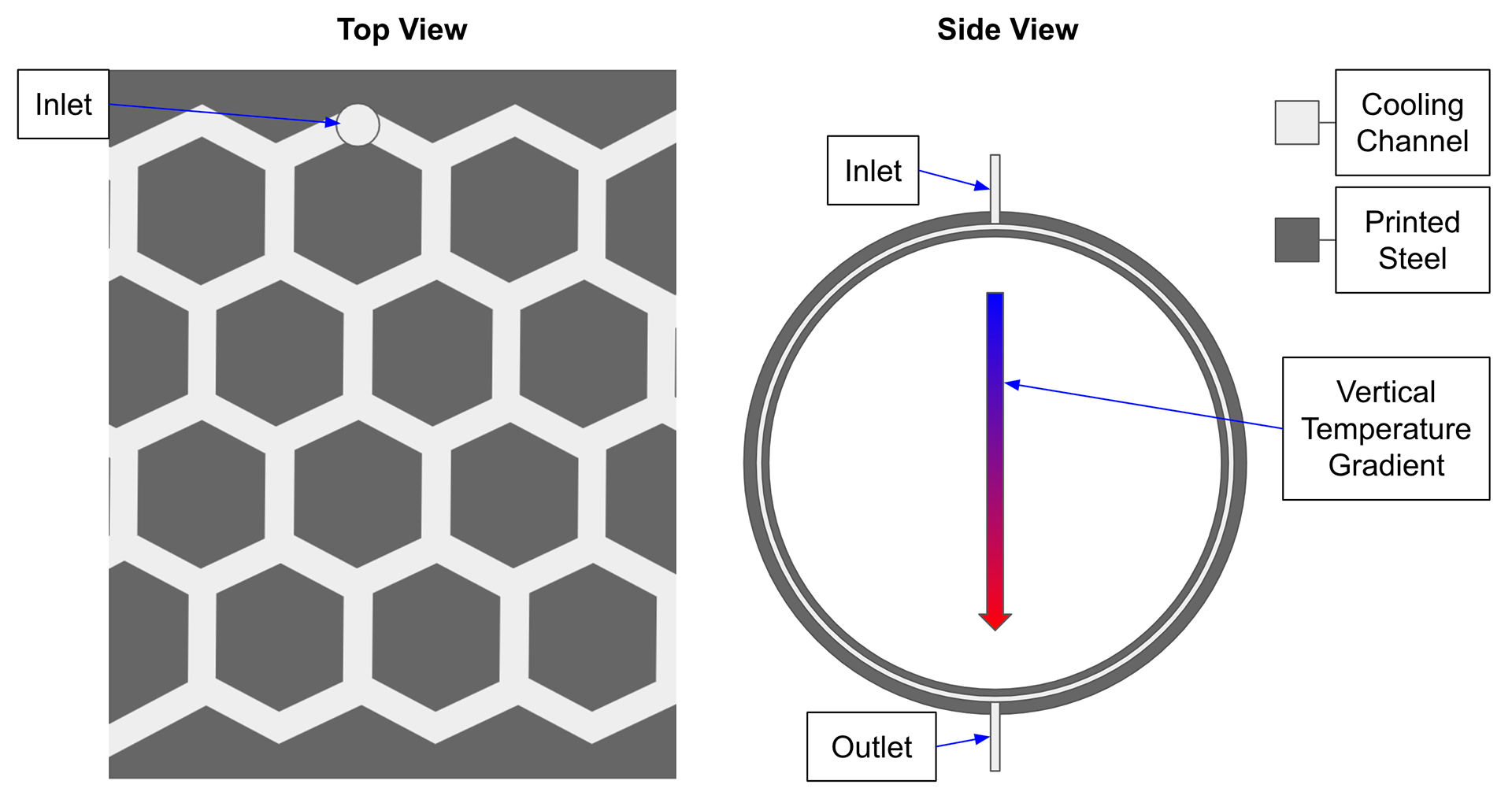
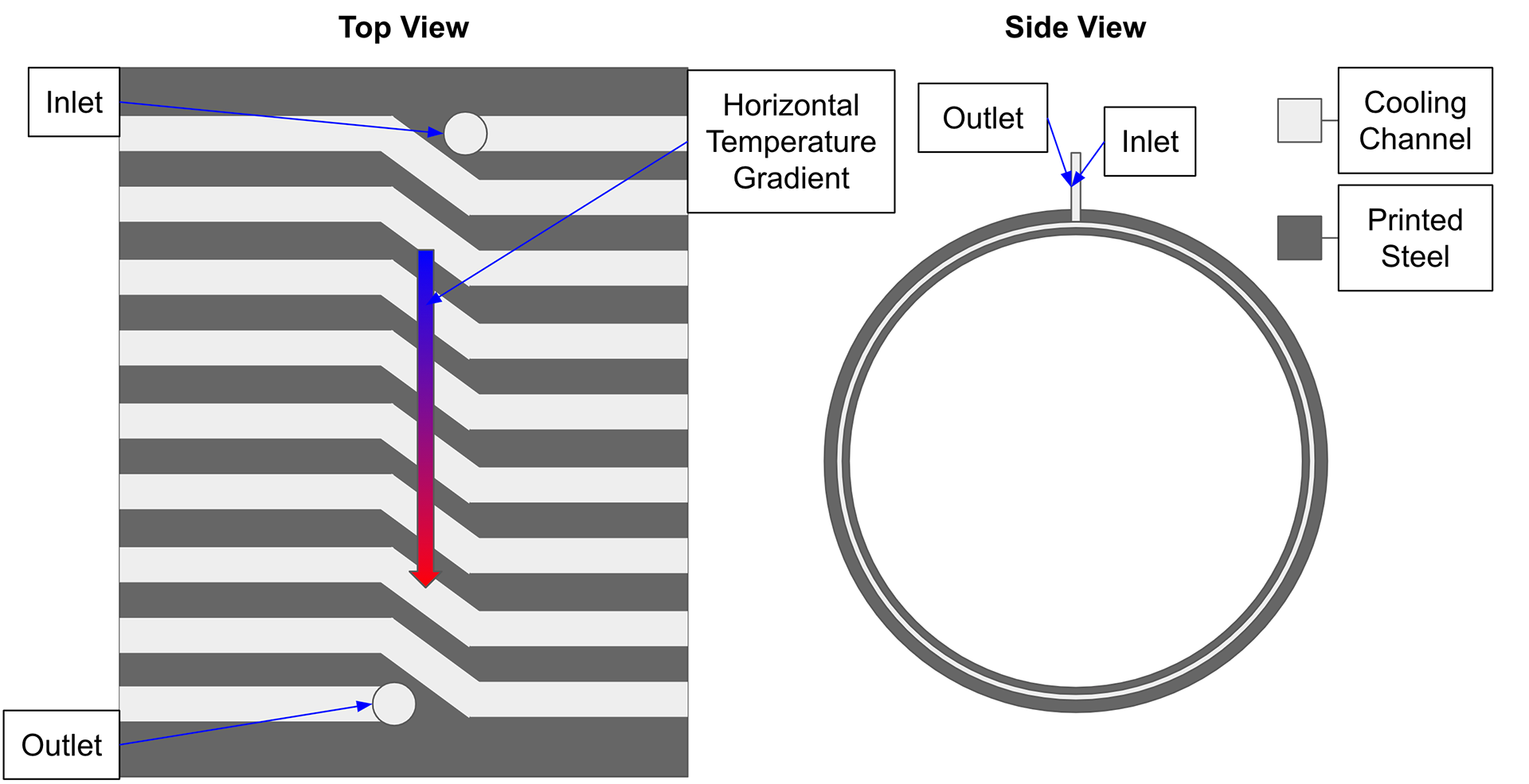
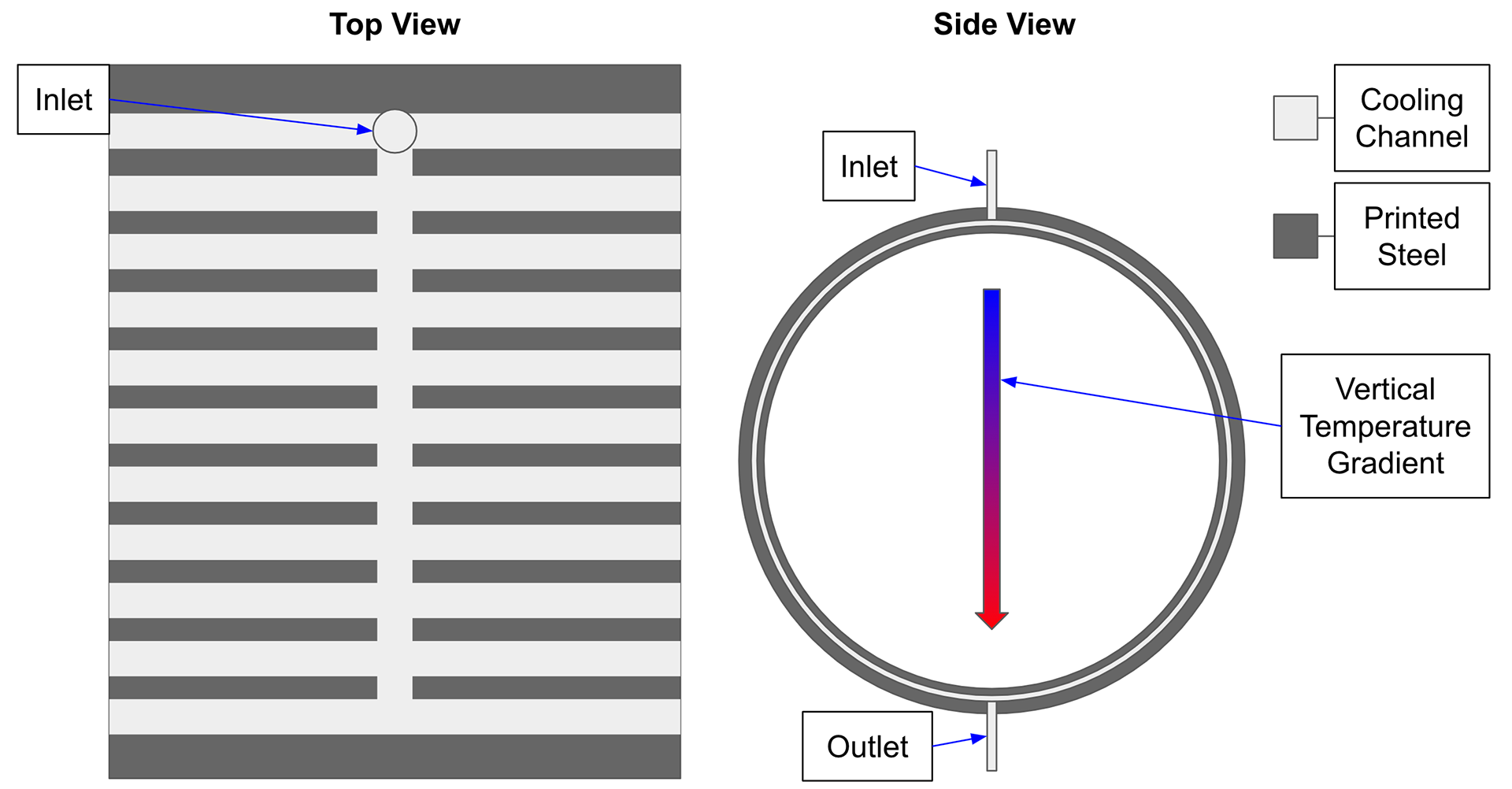
Computation Fluid Dynamics Parameter Sweep Simulation
After parametrically constructing the designs in SolidWorks, the next step was to conduct a CFD simulation. The relevant variables are shown to the left. The channel pitch and number of tubes were swept through a reasonable range of values, all other variables remained constant.
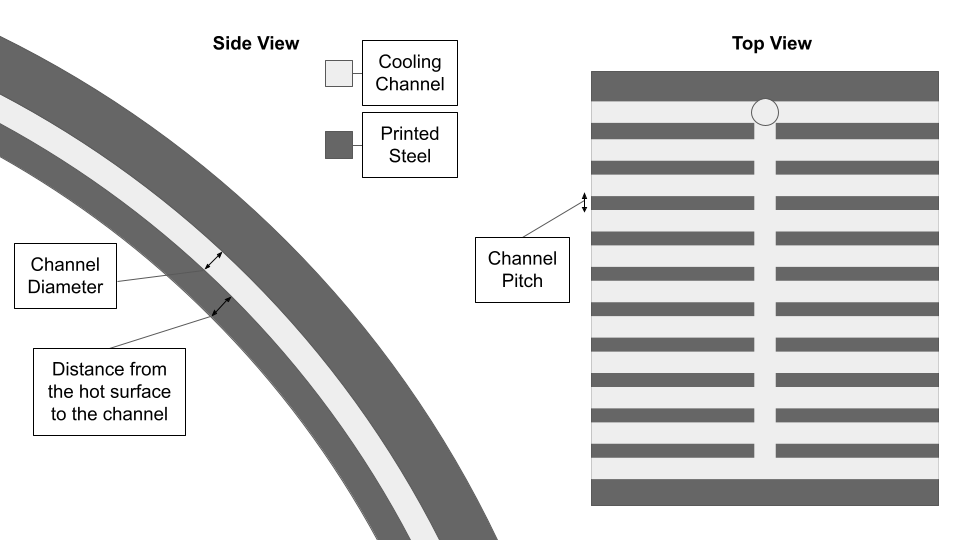
Mesh Verification
In order to find an appropriate mesh size and validate the simulation results two mesh verification tests were conducted. The top row shows a velocity profile mesh test. The velocity profile within the tube at various mesh size vs an analytical solution is shown on the top left with the associated error shown on the top right. The bottom shows similar test with pressure drop in a section of straight tube.
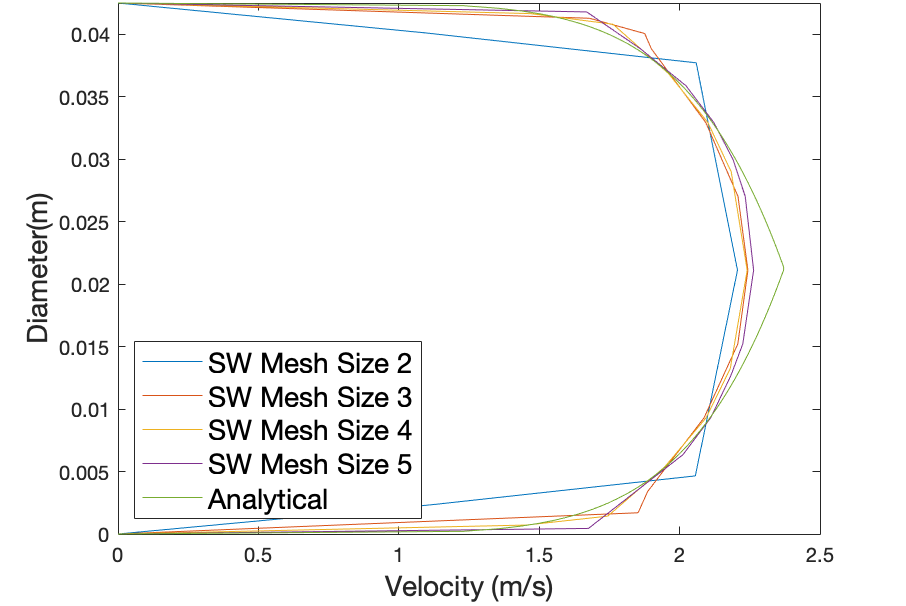
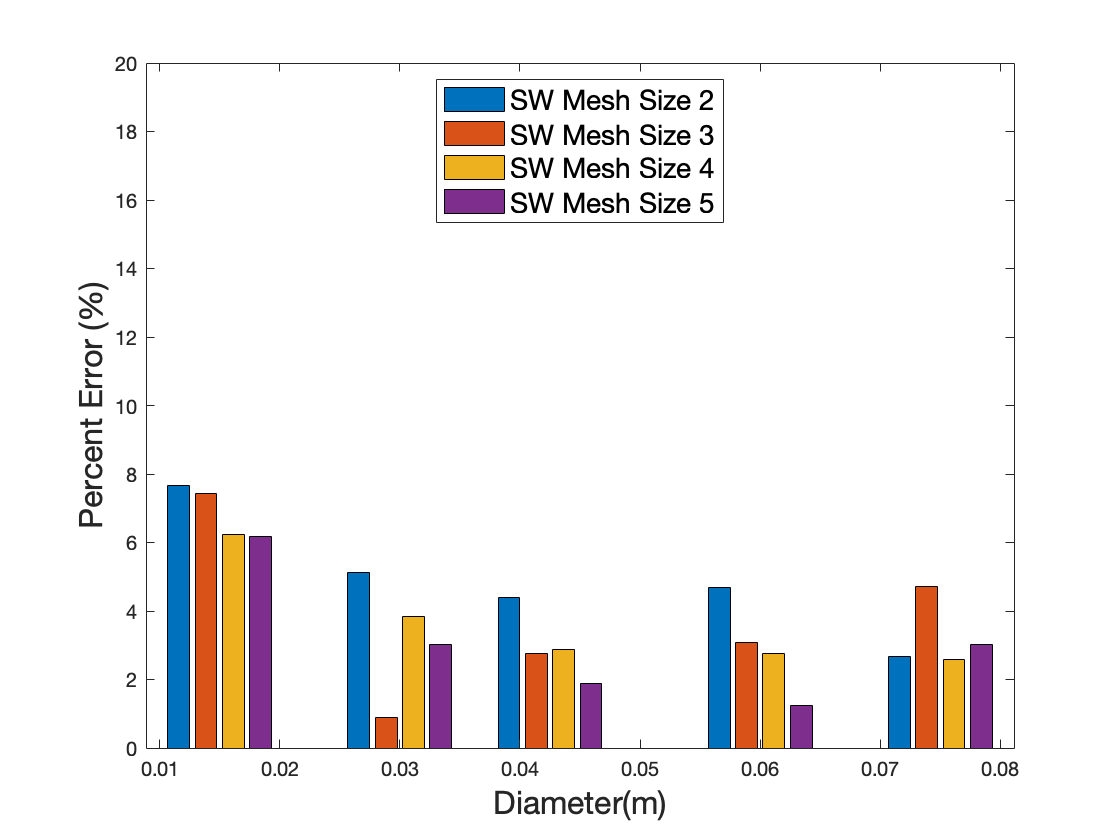
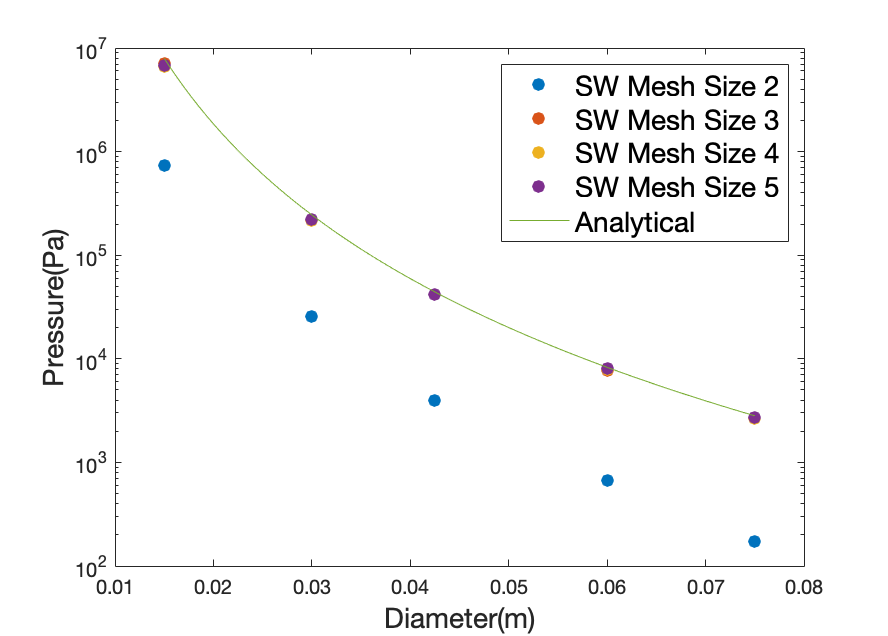
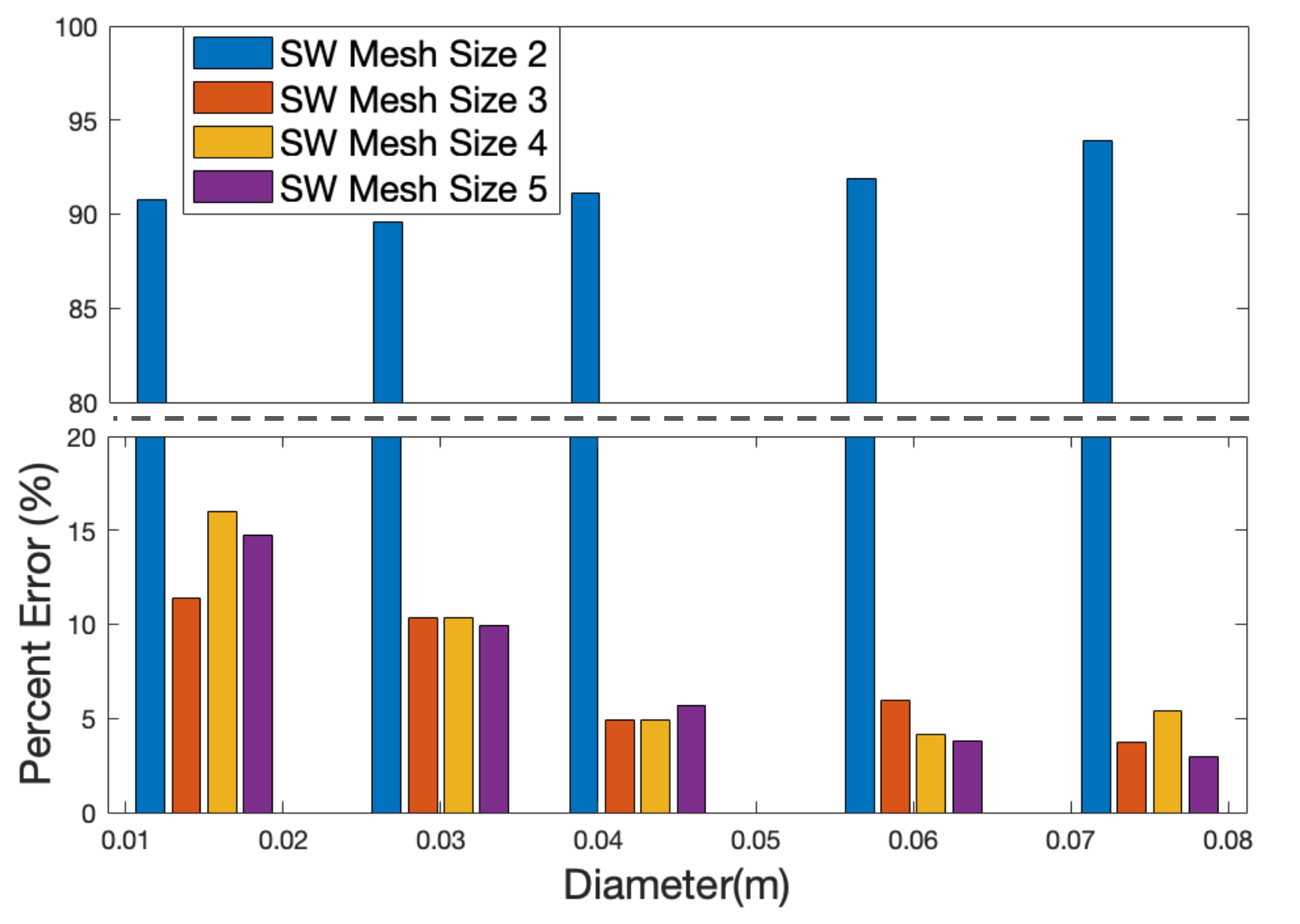
CFD Simulation Results
The series design at a cooling channel diameter of 30 mm achieved a maximum temperature of 31𝐶 with 15.7 kW of work. The series design had improved performance compared to the honeycomb and parallel designs because of the unrestricted coolant flow. The geometry of the others caused streams of fluid to overlap causing turbulence.
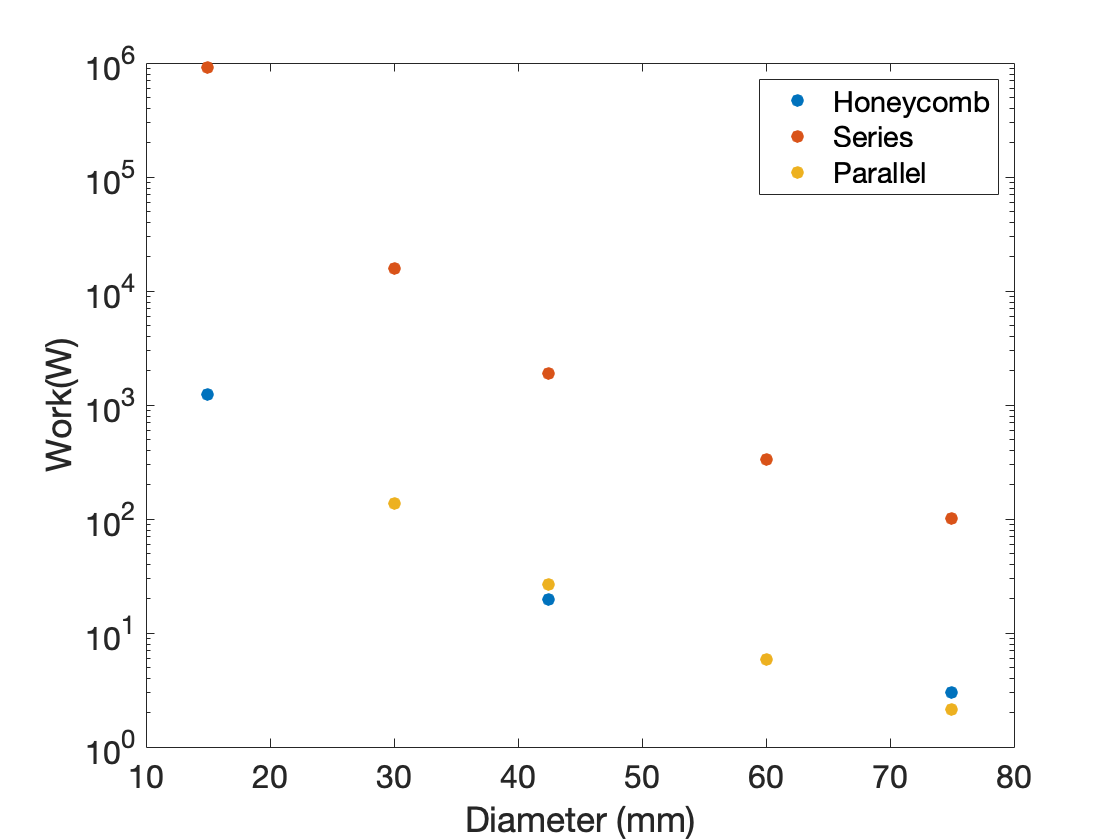
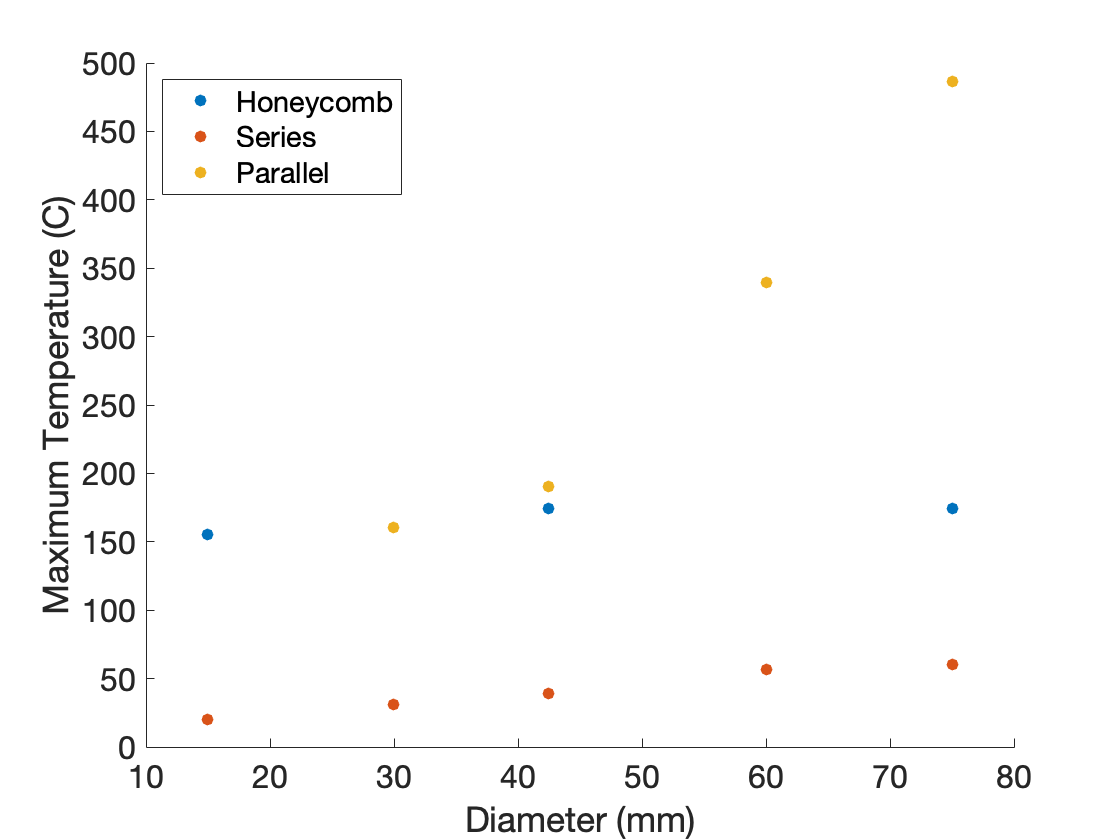
Heat Exchanger System Analysis
Two typical wind turbine heat exchanger methods, air cooling and liquid cooling, were examined using the effectiveness Number of Transfer Units (NTU) method. Important to the effectiveness of heat exchangers is their size. For this analysis, the heat exchangers were sized using the Log Mean Temperature Difference method. On the left is a salt-water cooled shell and tube design and on the right is an air cooled circular finned tube design.
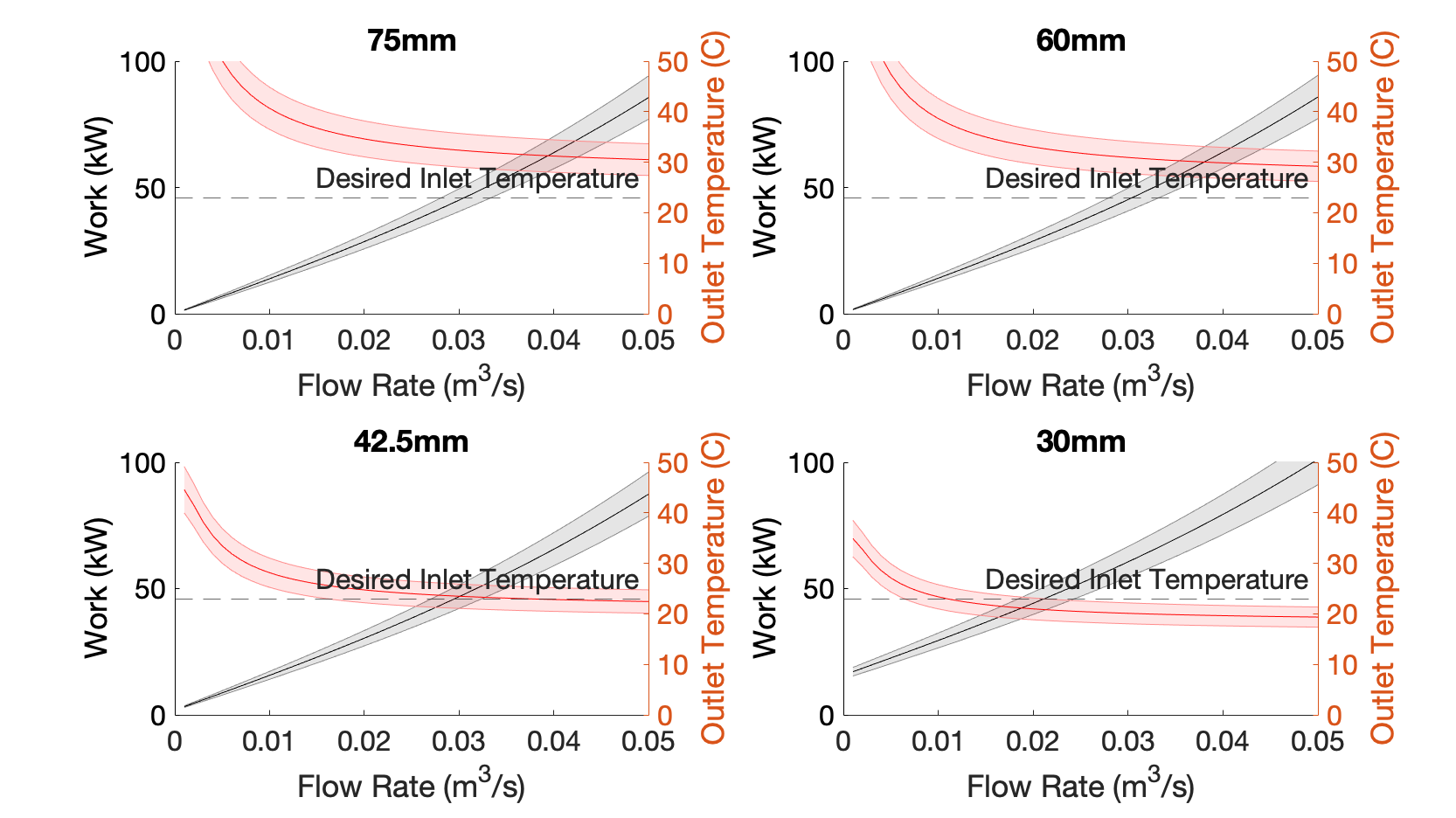
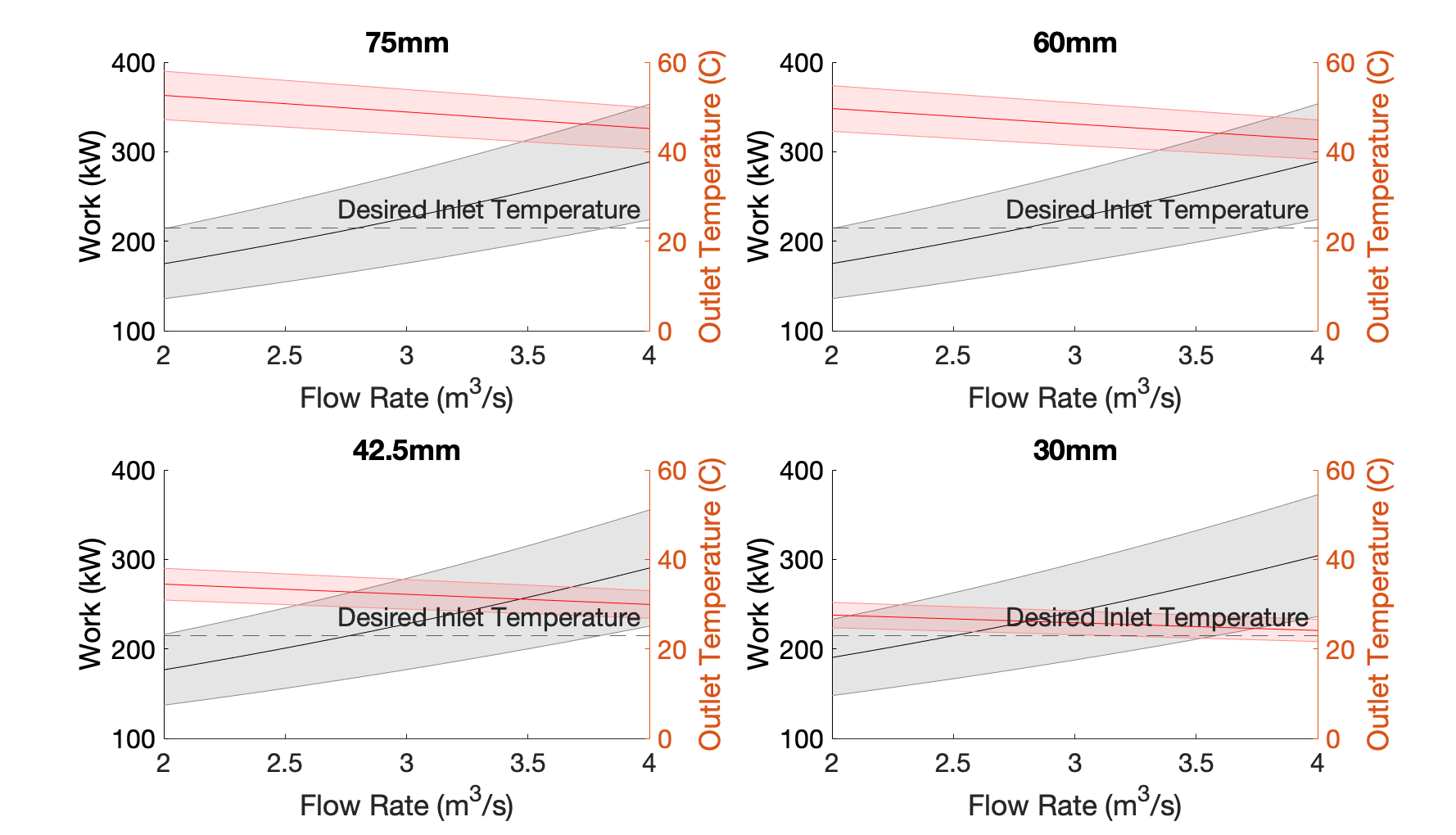
The results of the heat exchanger analysis make it clear that a shell and tube heat exchanger with seawater coolant exhibited improved performance over an air cooling option. Seawater coolant takes advantage of higher heat capacity, density, and thermal conductivity than air, all factors which lead to higher heat transfer coefficients when compared to liquid-air cooling.
This work was turned into a conference paper that can be viewed here: https://asmedigitalcollection.asme.org/POWER/proceedings-pdf/POWER2022/85826/V001T15A003/6920337/v001t15a003-power2022-85155.pdf