Summary
Sector: Renewable Energy
Software: SolidWorks, Matlab
Manufacturing: Sheet Metal, Laser Cut, 3D Printing
Project Time: 3 weeks
A deployable vertical-axis wind turbine capable of storing down in a compact cylinder for easy transport and then deploying on site. The goals of this project were to:
1. Incorporate developable mechanisms
2. Gather proof-of-concept data
Happy to update: project was awarded as a finalist at the national ASME Student Mechanism and Robot Design Competition and the work was included in a paper for the Journal of Mechanical Design: https://asmedigitalcollection.asme.org/mechanicaldesign/article-abstract/146/1/013301/1166779/Design-Considerations-for-the-Dimensional?redirectedFrom=fulltext
Design Process
The prototype began with the design of the four-bar linkage mechanism that would deploy the wings. These mechanisms conform to the cylindrical base of the turbine and therefore are considered developable mechanisms. I used a graphical method to design them.
Next, I began sketching designs, talking with colleagues and making small iterative prototypes.
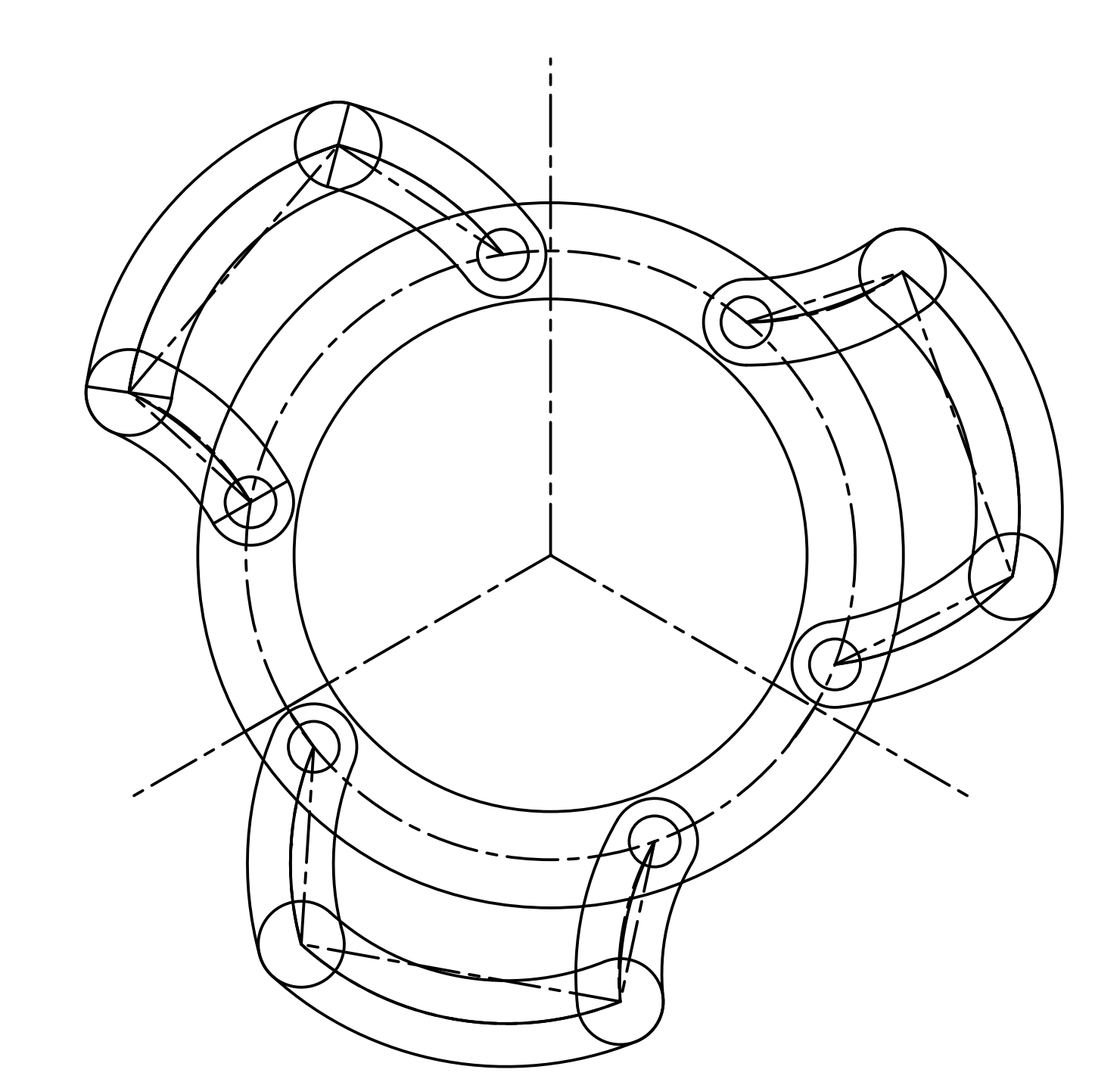
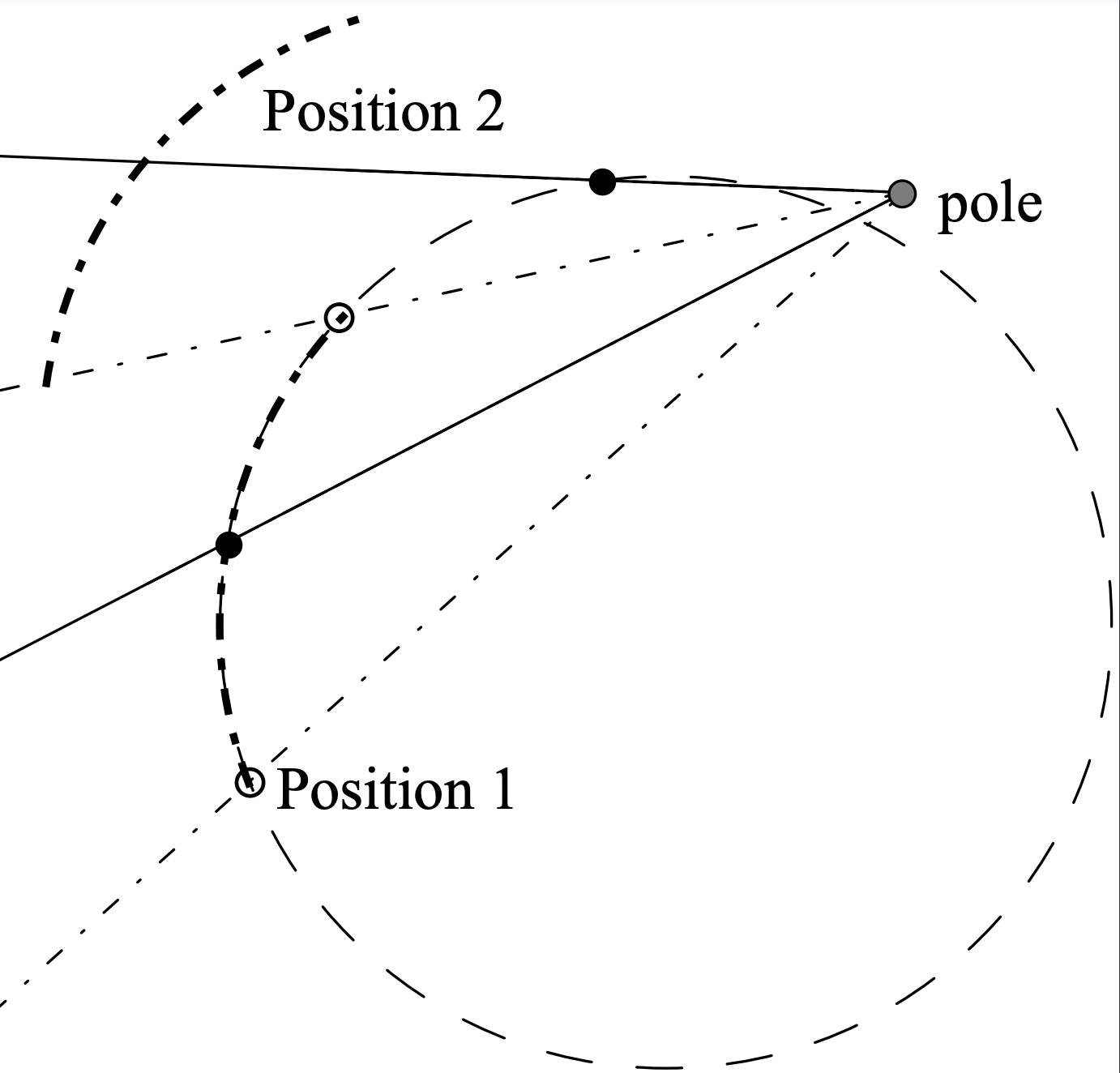
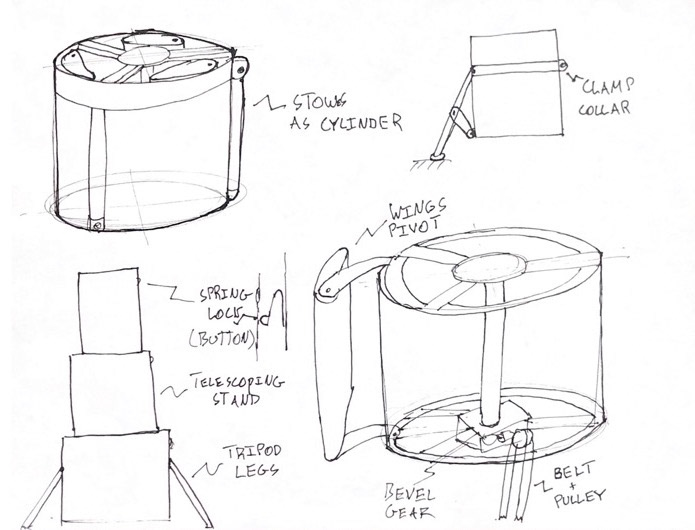
Iteration
I started with a simplified 3D printed design. Using LEGO joints as pins and taking an existing telescoping tower design for a quick mock up. This gave me ideas on the pin-join design and telescoping tower.
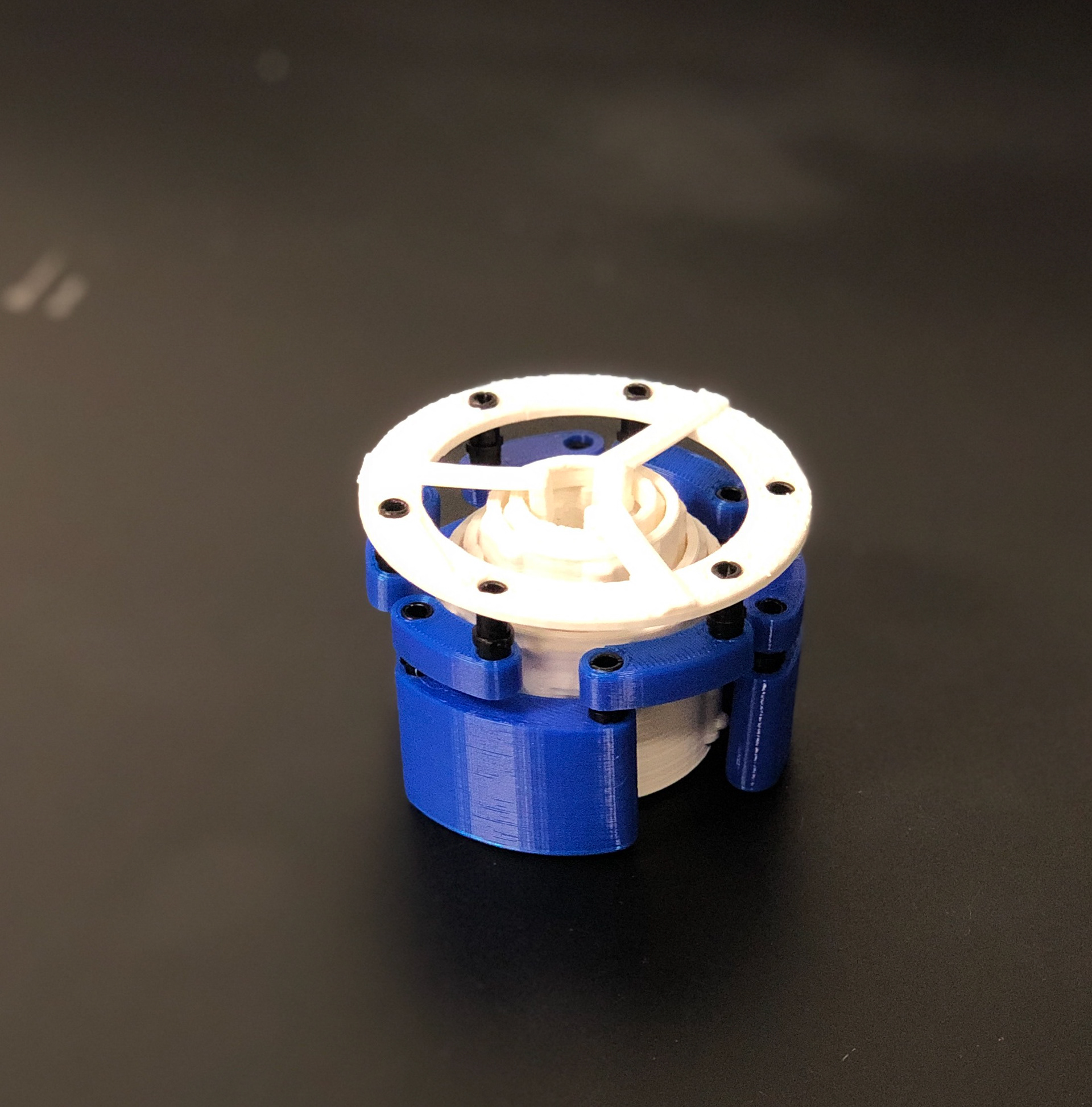
Next, I began building a larger iteration with wooden linkages, and many bolts, too many bolts. I learned that I could make a cleaner design with 3D printed linkages. I also iterated upon the wing design. I experimented with different methods of fastening and materials. With the scale and low forces, a 3D printed solution with glue ended up being the most straight forward solution.
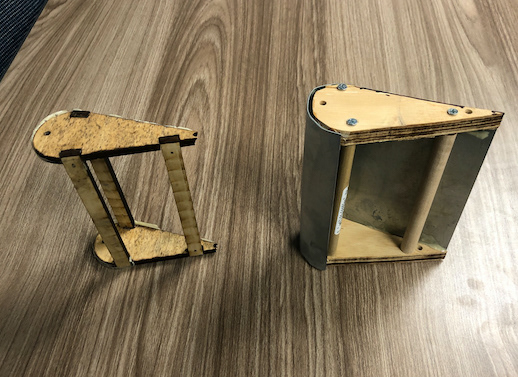
Solution
This iteration stows into a perfect cylinder meaning many of them could be efficiently stacked like soda cans and then deployed onsite where they are needed the most.
It's not only cheaper and easier to ship and deploy than competitors but it's easier to maintain because the components prone to fatigue failure can be lowered to the ground, replaced, and raised again.
What I would like to improve upon for the next iteration:
+ High-speed bearing
+ Automated telescoping base
+ Fiber composite wings
+ Locking four-bar mechanism
+ Analysis: FEA for structural components and CFD to compare with experimental data
+ Field testing and fatigue testing
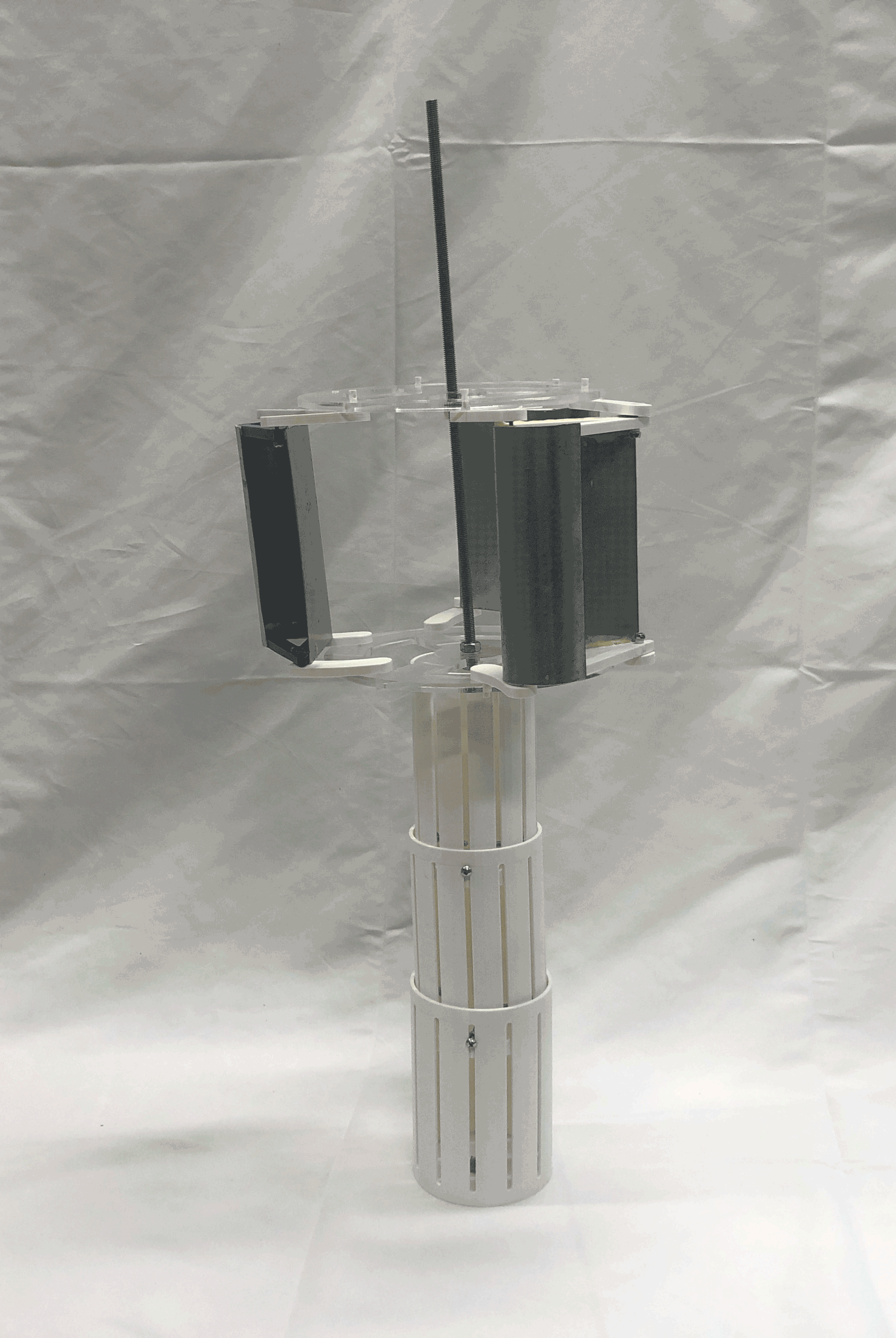
Testing
Testing was done to provide proof-of-concept data, meaning the data does not provide meaningful results in terms of efficiency expected, aerodynamics of the blade design, or fatigue testing. It does however validate that this new wing design would work as an electricity generating turbine and is comparable to existing designs.
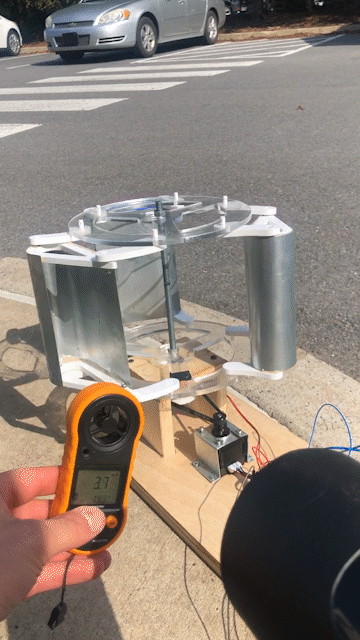
2nd Iteration Prototype
This second prototype was built with my brother over the course of a few months, we included the following features:
+ High speed bearings
+ Sheet metal linkage and frame design
+ Increased swept area (.35m^2)
+ High speed bearings
+ Sheet metal linkage and frame design
+ Increased swept area (.35m^2)
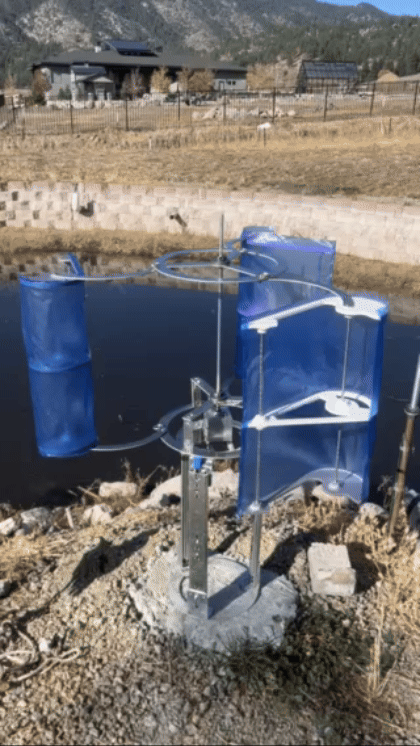
Failure Analysis
A storm blew the prototype over, in order to better understand the forces involved a simplified free body diagram is created. Several assumptions are used but the exercise provides a sanity check for the changes needed to prevent failure in the future.
Fd = (1/2) * ρ * Cd * A * v²
σ = My/I , Area moment of Inertia I of an L-bracket is shown below.
Basic calculations show a factor of safety, FS =.25 with the current bracket design.
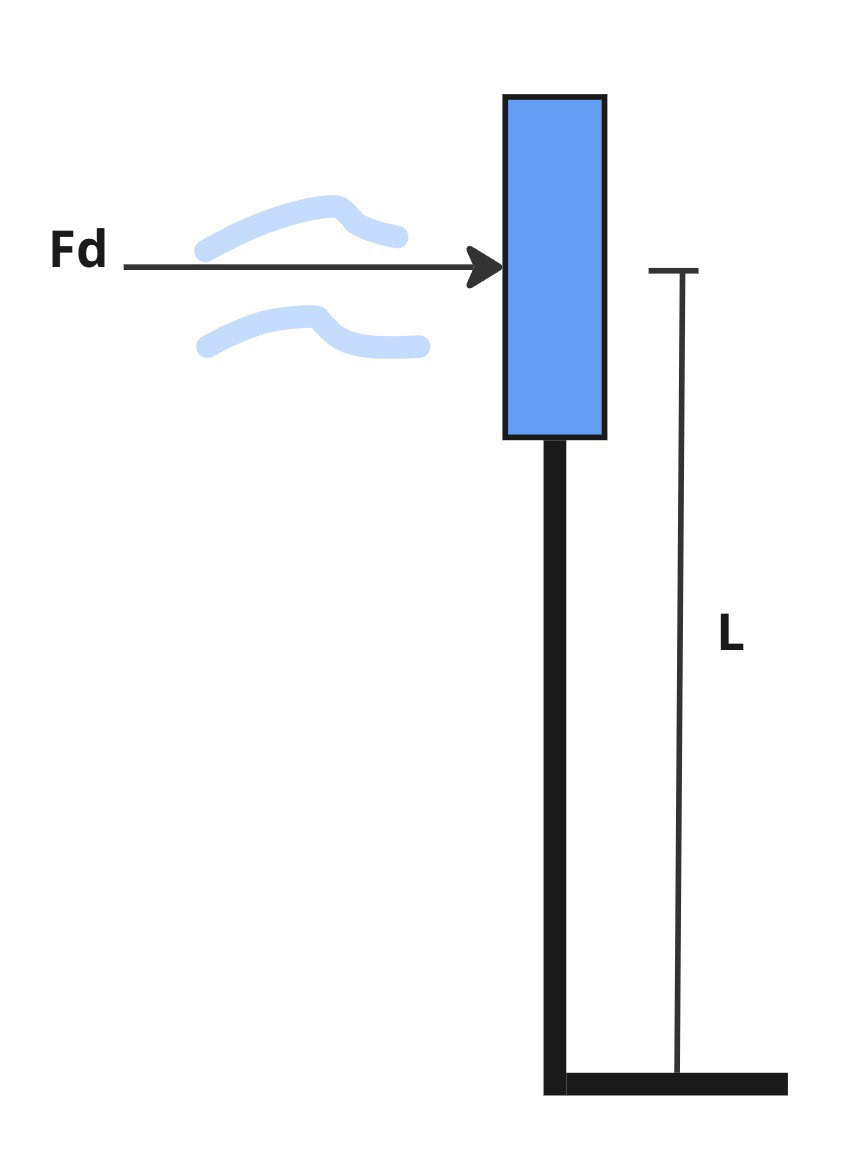
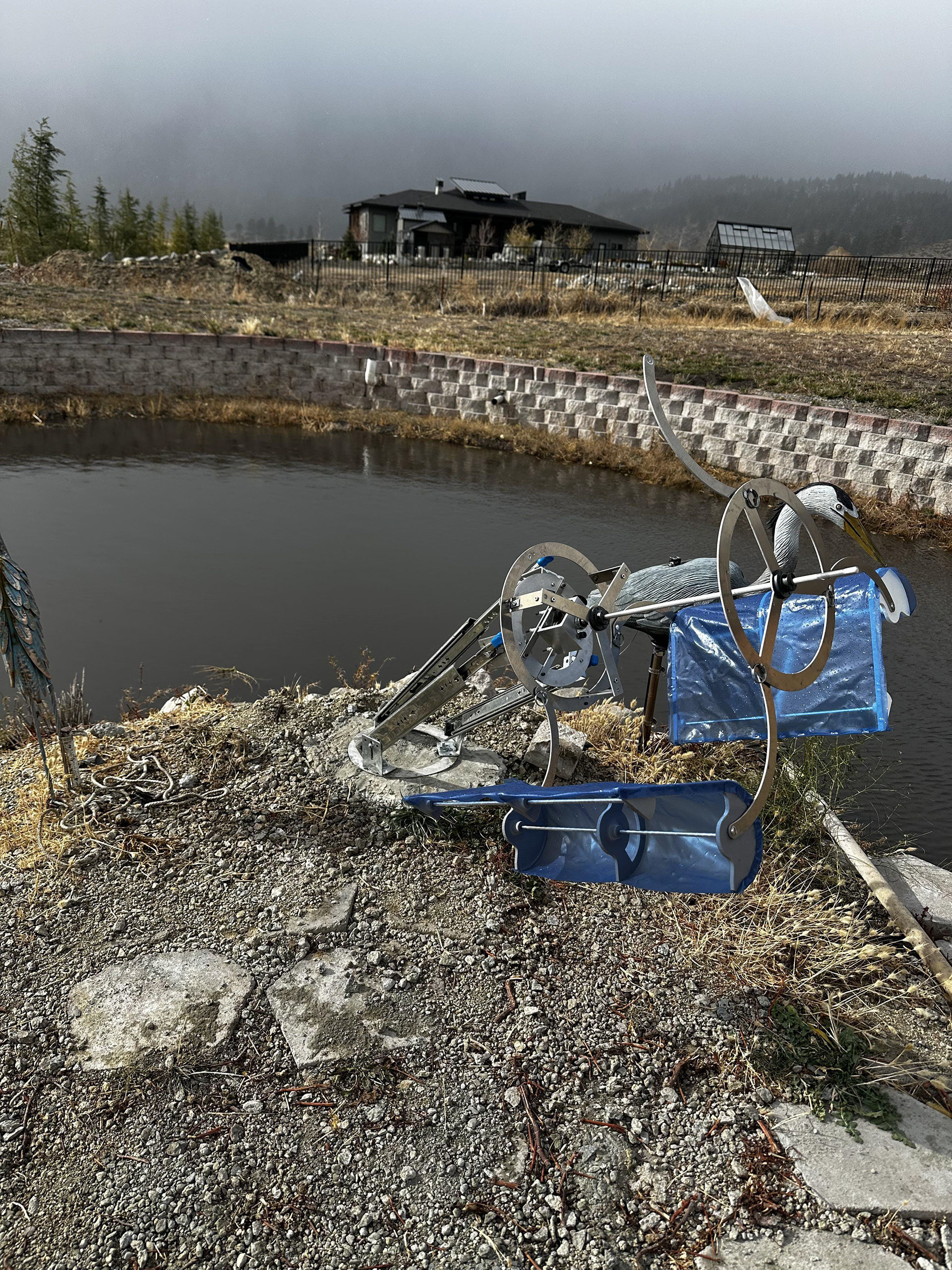