Summary
Sector: Industrial Robotics
Software: SolidWorks, Python
Manufacturing: CNC, 3D Printing, Laser Cutting, considerations for Injection Molding
Project Time: 5 weeks (6 month internship)
During a 6 month co-op with PA Consulting, I worked on a humanoid industrial robot. I aided in tolerance stackup analysis, FEA, cable routing and more. This page specifically showcases a latching system I designed for the robots main power and data cables.
Device requirements:
1. Retain electrical cable conduit during robot's actuation
2. Allow for full range of motion of the robot
3. Maintain ingress protection rating (IP 65)
4. Locate conduit along its length
5. No tools required to lock and unlock
6. Withstand 200lbf static load
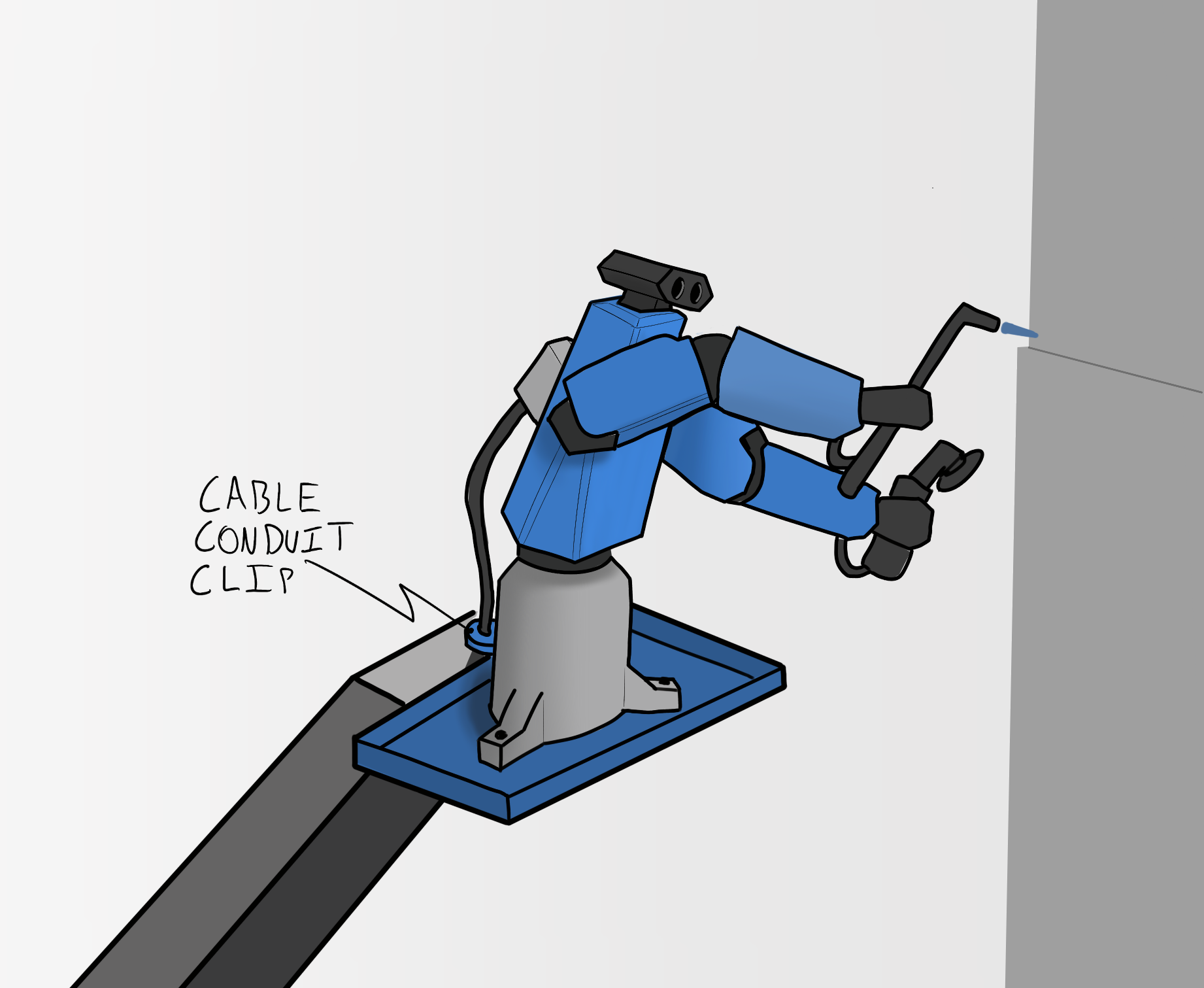
Design Process
The design began with defining the requirements and translating them into specifications. For example, two requirements: 2. Allow for full range of motion during actuation and 4. Locate conduit along length were not well understood. To learn more I prototyped using a bicycle wheel, off the shelf clips, and an office chair. From that I learned:
• 17” - 24” conduit length required
• Must allow for axial rotation
• Cables fit and don’t add stiffness to the conduit
A sketch of the rapid prototype is shown on the right.
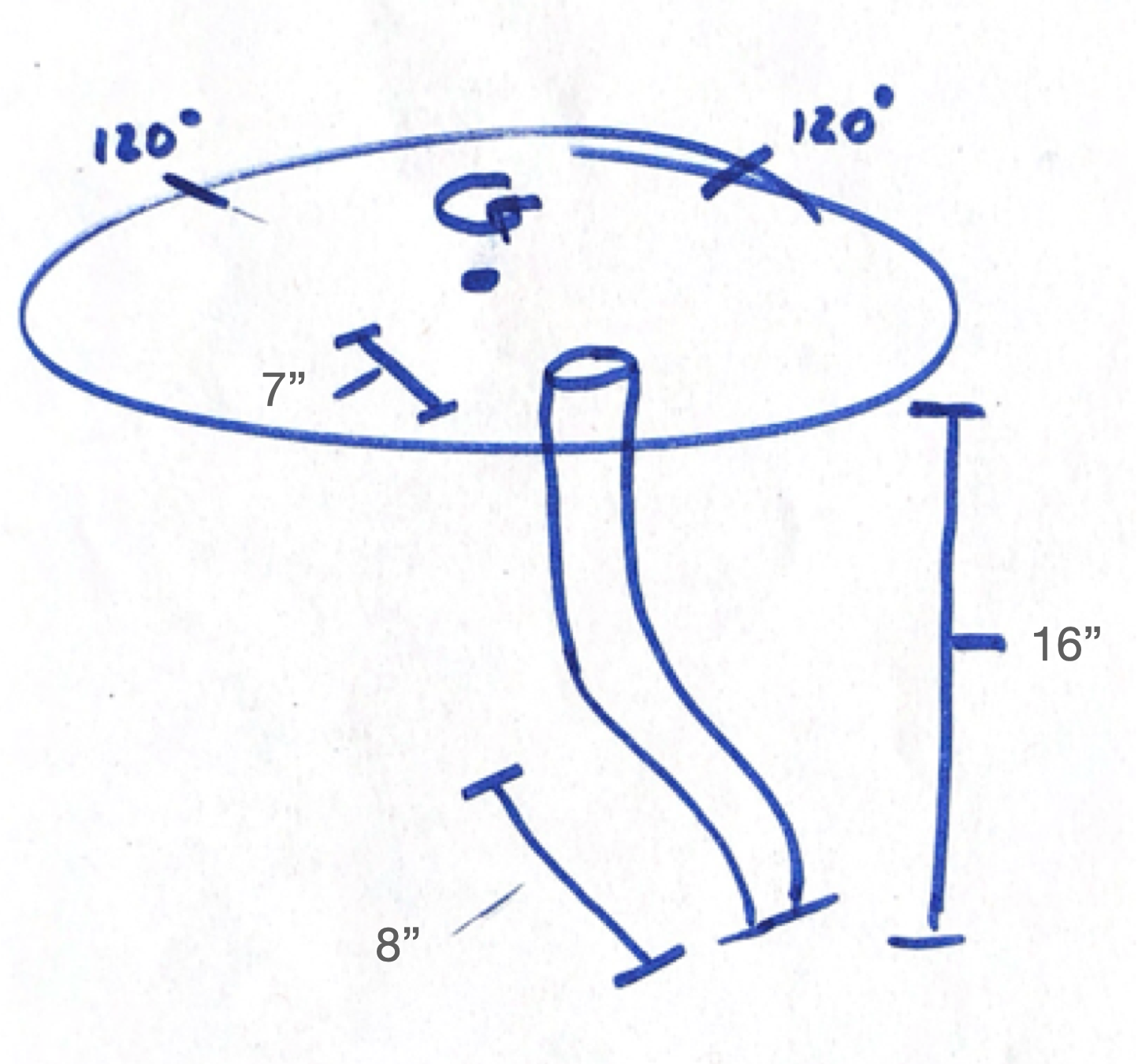
Iteration
Next, two different supports were designed based on competing trade offs and shifting design parameters. The support needed to fulfill the following requirements: 3. Maintain ingress protection rating (IP 65) and 6. Withstand 100lbf static load.
The left was designed using cantilever beam hand calcs, had little internal room for the bracket and major ingress protection complications which would involve sealing fasteners, o-ring clip, locating feature.
For the right I incorporated ribs and a thicker injection molded housing which FEA showed resultant factor of safety of 1.3 and no ingress. Making it viable to move forward with.
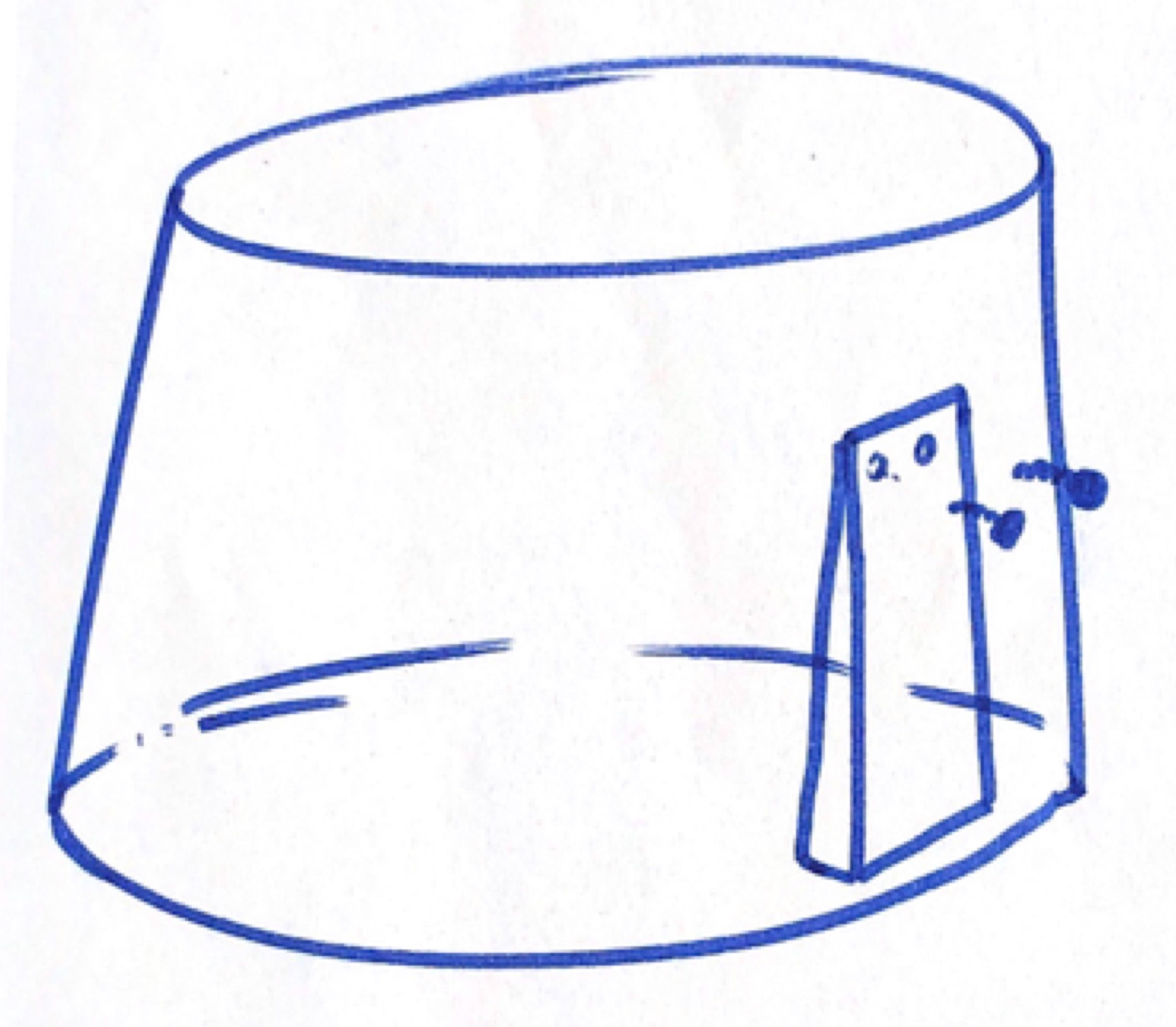
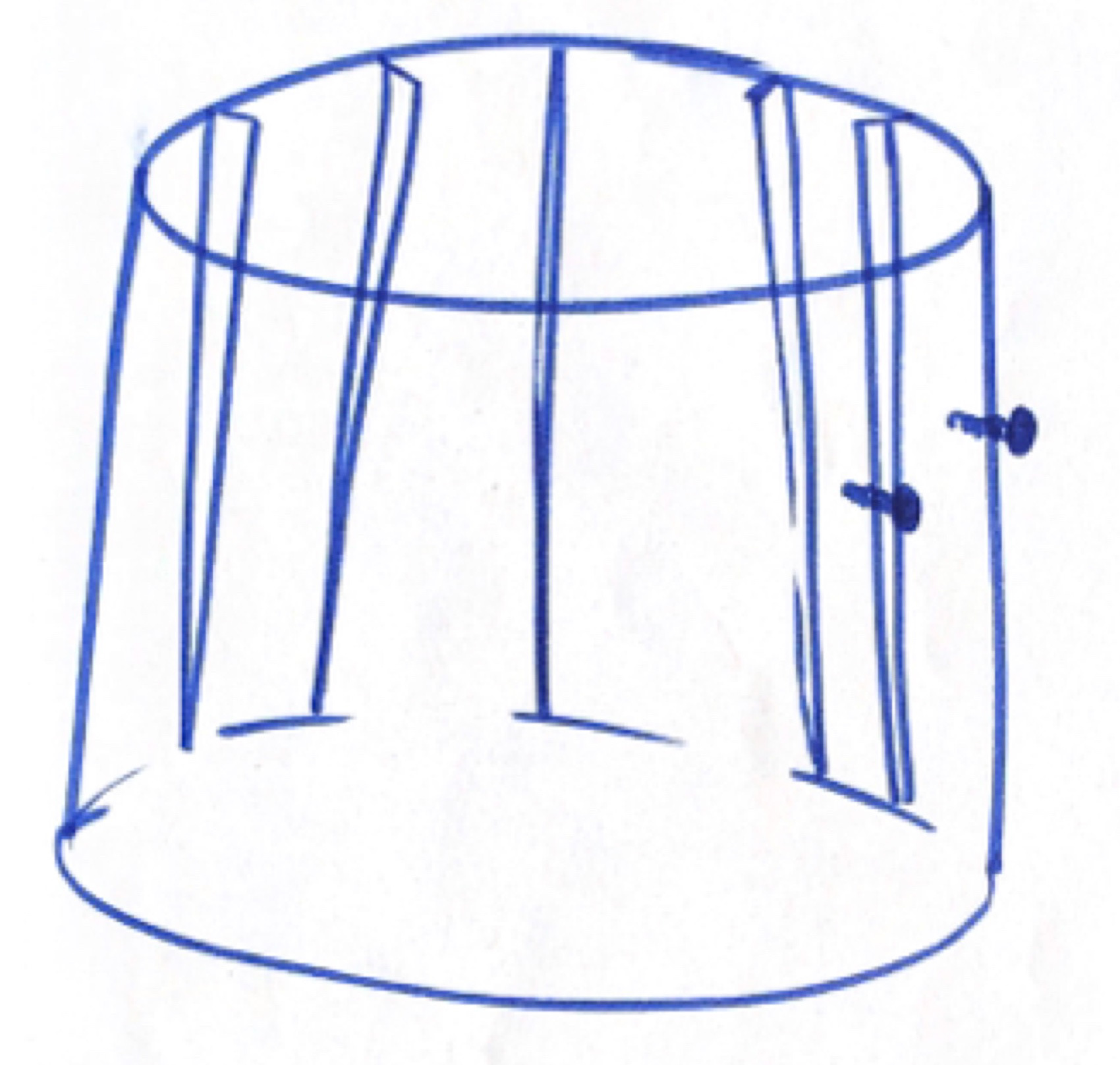
Solution
The electrical conduit latching system used a cam to compress a piece of rubber and create spring locking action. It fulfills all of the requirements and gave me experience with DFM and DFA through injection molding, tolerances, poka-yoke, material selection, etc.
It was a fun project with the most puzzling pieces being the support structure and cam handle. The final result was a sturdy and easy to use clip that securely fastens the robots’ cable conduit.
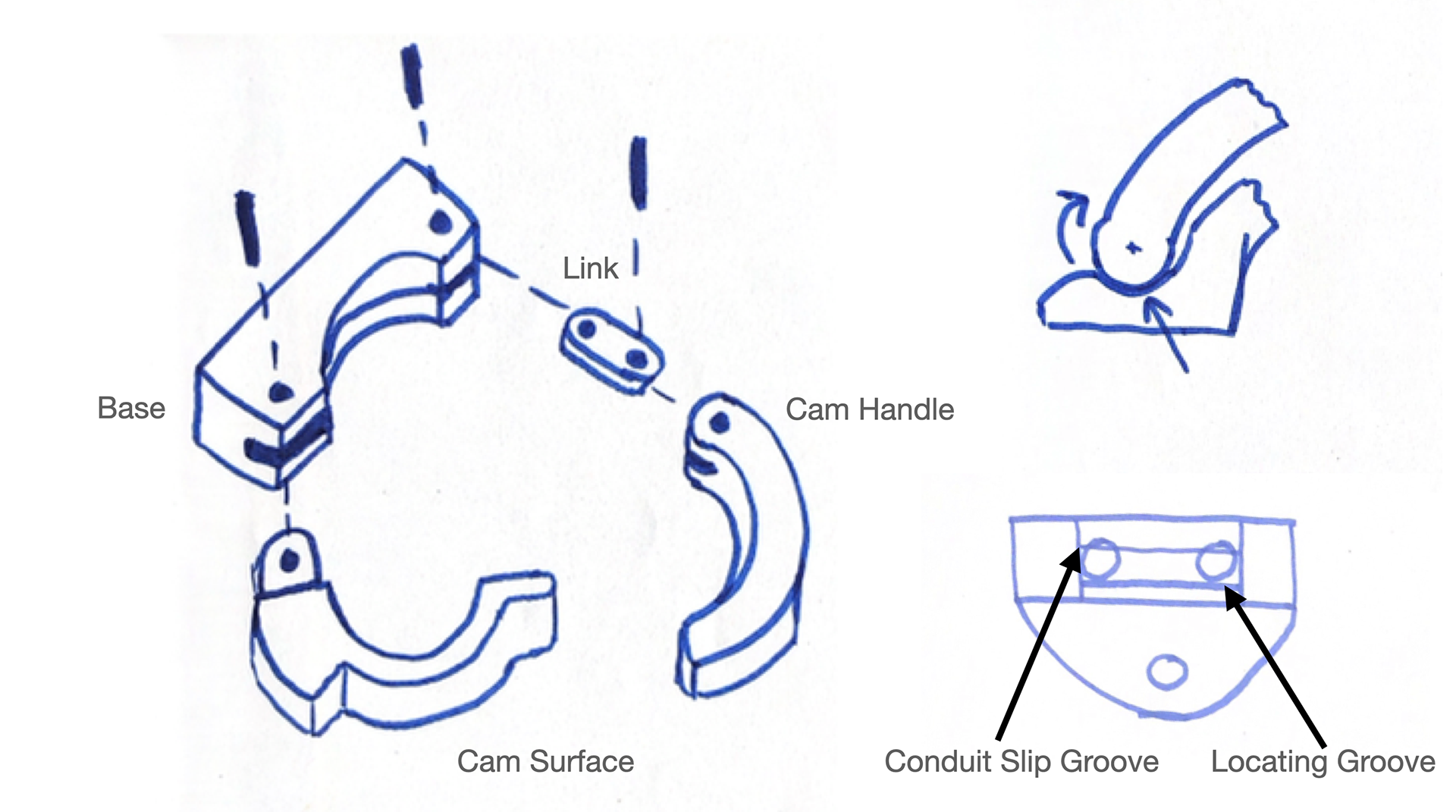